Industry 4.0
Connectivity = Productivity
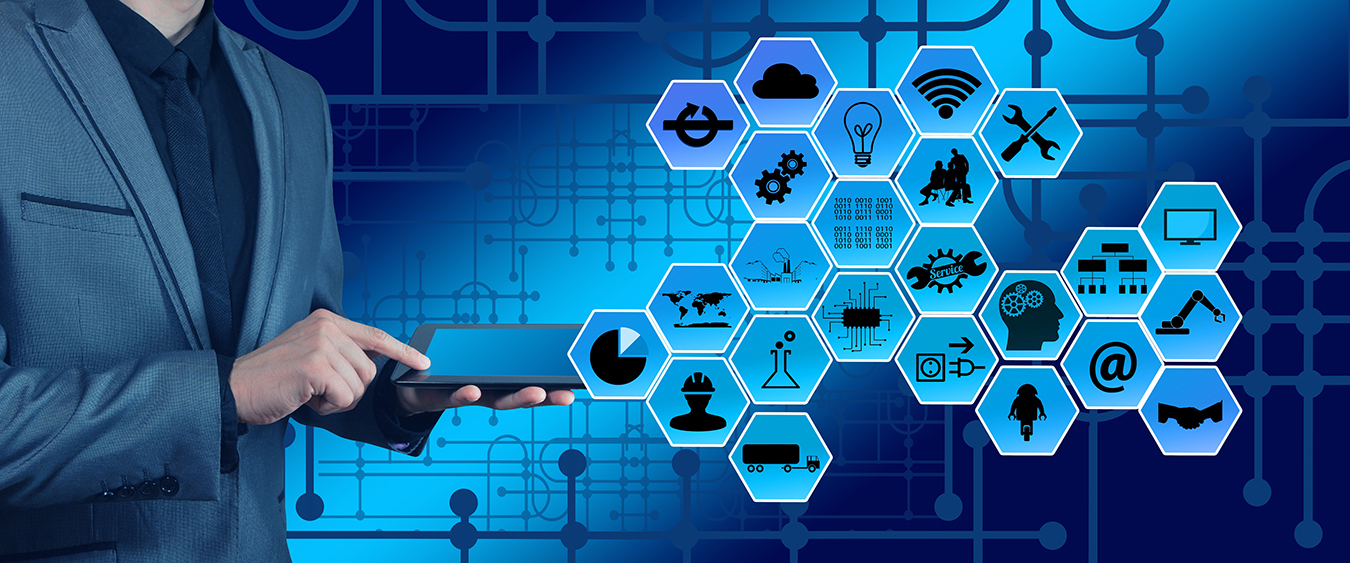
Connectivity
• Those productive machines that allow it can be connected. It is mainly designed for machining centers.
• It has to be understood as a complement to the PQM system. The method of working with the PQM system must first be matured.
• Capture data and machine parameters during the machining process.
• Comparing these parameters with the variation in machining conditions allows processes to be improved and productivity increased.
Basic functions
• Monitoring of the machining status of the machine at the current moment.
• Statistics of the state of the machine by day and by hours. Time that has been machining, in preparation etc.
• Machine performance in different shifts or types of work.
Advanced features. They are the ones that really improve productivity
• Measurement process.
• Process for determining machining strategies for possible improvement.
• Improvement process.

Measurement
• Detailed times of the manufacture of a piece. Cutting times, G1, G0, tool change, etc.
• Machining power with every tool.
• Number of times the tool changes and how long it takes in each case.
• Time in which the machine is actually machining.
• Total manufacturing times for a part.
Improvement process
• Optimum power of the tool. Determine if the tool is used at optimal power or can be raised for next parts.
• Change process, minimize operations, use different tools, different machining strategies and find the optimal process.