Lean Manufacturing

Systematic elimination of waste
• According to the "Just in Time" philosophy, nothing is manufactured until it is necessary, always meeting customer expectations.
• The limit of this principle: only when a product is withdrawn will a new one be manufactured.
• To lower the cost, you have to eliminate all those tasks that do not add value to the product. Waste must be avoided.
• Lean manufacturing is about the systematic elimination of waste.
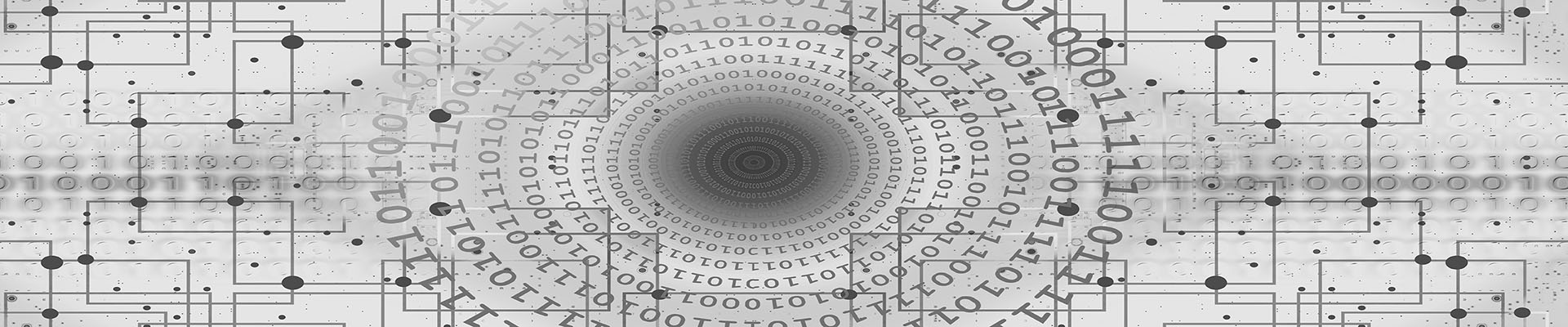
Seven types of waste are distinguished
• Overproduction: produce innicesary products, when they are not needed and in quantities greater than required.
• Inventory: materials stored in the form of raw materials, semi-finished products and final products. It is considered an unnecessary expense, given the cost of personnel and space that derives.
• Movements: In many cases, employees waste a lot of time doing things that do not add value. Looking for information, tools, not having a clear procedure, leaving parts in an undefined area and then having to move it more often.
• Waiting: machine preparation times to make different parts, waiting for poorly coordinated jobs...
• Transport: time lost in inter-zone transports or subcontracted transports.
• Unnecessary processes: making complex products of convoluted design is a waste. Customers will only pay for features they value. Avoid unnecessary processes.
• Defects: inferior quality products mean a waste of time and resources, require more inspection processes and repetitions of inspection processes and repetitions of processes. They disrupt the normal production process.
• Inactivities: downtime of the machine or the operator.
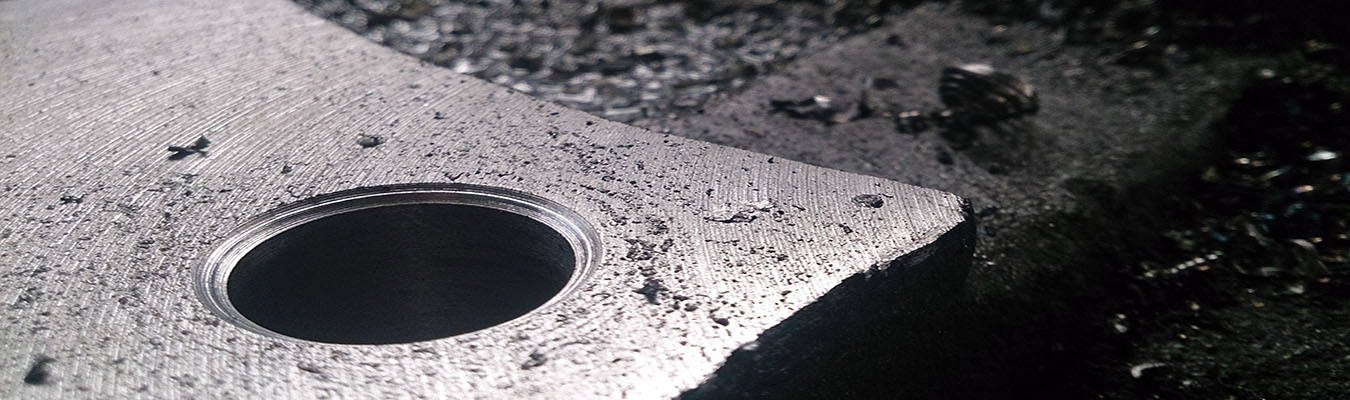
PQM software is a very powerful tool that allows you to work in a very efficient way, eliminating as much as possible the waste produced in the manufacturing process.